Hybrid Polymer Capacitors Technology Trends
June 28, 2019
Preface
Aluminum non-solid electrolytic capacitors (electrolytic capacitors) are used in many electronic devices as inexpensive, small-size, and large-capacitance devices.
However, electrolytic capacitors have higher resistance than other capacitors and their characteristics are sensitive to temperature. Especially in the low temperature range, the increase in the resistance and the decrease in the capacitance are remarkable, making the it not suitable for equipment used in low temperature.
In order to overcome this weakness, the development of electrolytes mainly affecting the electric characteristics has been extensively carried out. Now, electric characteristics of electrolytic capacitors have been improved, and longer life-time, lower resistance, smaller temperature dependence have been achieved, leading to considerable improvement of their performance. As a result, their adoption has been expanding in devices, such as in-vehicle, industrial, communication devices, and others requiring high reliability in a wide temperature range.
For in-vehicle equipment, the extension of functions has progressed in recent years mainly for safety systems such as advanced driving assistance system (ADAS) and for the full-scale introduction of automatic driving. In addition, as environ-mental regulations become severe, computerization of vehicles has been advancing. For this reason, the number of electronic control units (ECUs) mounted on in-vehicle devices has also increased significantly. Conventionally, in-vehicle ECUs are installed in a cabin space free from significant temperature variation and strong vibration. However, for the purpose of securing sufficient cabin space and reducing wire harnesses, installation in the engine room has become popular.
The temperature and vibration environment inside the engine room is more severe than inside the cabin. Therefore, the capacitors mounted on ECUs are required to have higher temperature and vibration resistance than before.
Moreover, demands for space saving, weight reduction, and power efficiency for in-vehicle devices increase the performance requirements, such as miniaturization, lower equivalent series resistance (ESR), and higher ripple current, which cannot be dealt with by conventional electrolytic capacitors. In order to respond to these requirements, Rubycon Corporation has developed a high-performance hybrid capacitor based on the conventional conductive polymer aluminum solid electrolytic capacitor (conductive polymer capacitor) using its original hybrid technology, thus contributing to the high functionality of in-vehicle equipment.
This article introduces the technological trend of conductive polymer aluminum solid electrolytic capacitor (hybrid), which the company has developed up to now.
Development of Conductive Polymer Capacitor
Conductive polymer aluminum solid electrolytic capacitors use conductive polymers with excellent conductivity. They feature small temperature variation property and small resistance; can deal with high ripple current; and exhibit little aging of electric characteristics. Compared with an electrolytic solution, the conductive polymer has poor repairability of the dielectric fi lm. The upper limit of the rated voltage of the capacitors has been said to be 25V, making them less adaptable for in-vehicle ECUs.
The company elevated its development activities to solve these problems. As a result, Rubycon released in 2013 the PZA Series conductive polymer capacitors, which adopt an original polymer technology featuring high-purity PEDOT poly(3,4-ethylenedioxythiophene) and included a characteristic stabilizer and reaction inhibitor. The PZA Series features rated voltage up to 63V and maintains the characteristics of the conventional conductive polymer capacitor.
After that, the company has commercialized the surface-mounted PAV Series (105ºC product), which adopt the same polymer technology, and then the PZC and PCV Series (125ºC product), which guarantee high temperature operation, thus enhancing product variety.
Adoption of Original Hybrid Technology
The developed conductive polymer capacitors realize lower resistance, higher ripple current, and better temperature characteristics in comparison with the conventional electrolytic capacitor. However, its size is slightly larger and the electrostatic capacitance remains smaller as shown in Table 1. It incorporates a characteristic stabilizer with the function of repairing the dielectric film. In comparison with the electrolytic solution used in the electrolytic capacitor, however, the film’s repair-ability remains small. Therefore, the product with the same rated voltage has to use an anode foil with a voltage resistance higher than the electrolytic capacitor. As a result, the conductive polymer capacitor has a capacitance smaller than the electrolytic capacitor.
Series | PFV (Conductive polymer hybrid type) |
PCV (Conductive polymer Capacitor) |
TGV (Non-solid Aluminum Electrolytic Capacitor) |
---|---|---|---|
Capacitance(µF) | 330 | 100 | 330 |
Size (ΦD×L:㎜) |
10×10.5 | 10×12 | 10×10.5 |
ESR (Ω/100kHz) |
0.02 | 0.03 | 0.12 |
Ripple current (mA/100kHz) |
2,000 | 2,000 | 550 |
Lifetime (hour/125ºC) |
4,000 | 3,000 | 3,000 |
Example of performance comparison (25WV-Φ10 products)
In order to solve this problem, the company has developed a unique gel with a function of repairing the dielectric fi lm without hindering the performance of the conductive polymer. Adding this material — a process called hybridization — enables reduction of the withstanding voltage of the anode foil while maintaining the performance of the conductive polymer capacitor. With this technology, the company has developed PFV Series 125ºC hybrid capacitor that realizes the same high capacitance as the electrolytic capacitor. They were introduced into the market in 2015.
As the original functional gel does not contain ionic components, it does not affect the electrical characteristics of the capacitor. The electrical characteristics of the PFV Series are determined only by the performance of the conductive polymer. Therefore, it maintains stable electric characteristics from low temperature to high temperature, and with little change in aging characteristics over a long period of time (Figures 1 and 2), which are features of the conductive polymer capacitor itself
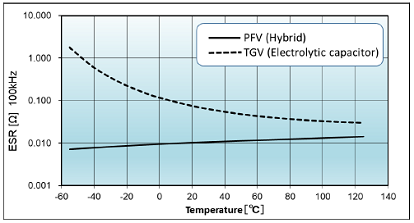
and the electrolytic capacitor: 25V 330µF (Φ10×10.5L)
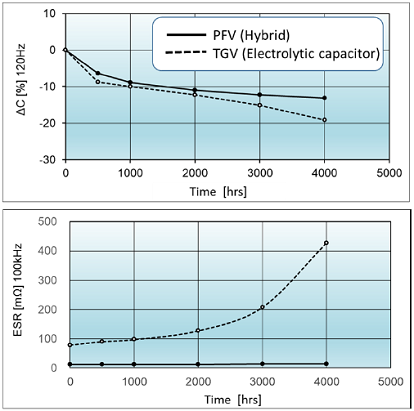
and the electrolytic capacitor: 25V 330µF (Φ10×10.5L)
Furthermore, the functional gel is thermally more stable than the solvent used for the conventional electrolytic solution. The amount of diffusion from the sealing rubber to the outside of the capacitor is one-third or less of the electrolytic solution. In addition, the gel also has a function of suppressing degradation of the conductive polymers. These contribute greatly to the long-term re-liability of the capacitor.
During the development of the PFV Series, the company has used the original hybrid technology, adopted a SMD type new sealing material having high heat resistance, and improved the manufacturing method. It has supplied a product line that guarantees operation at high temperature, such as the PHV Series at 135ºC guaranteed and the PLV Series at 150ºC guaranteed (Figure 3). Today, the company has further improved its original hybrid technology and newly developed the PSV Series compatible with high ripple current and 135ºC (Photo 1).
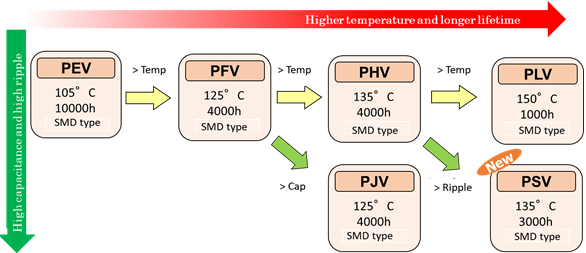
Features of PSV Series
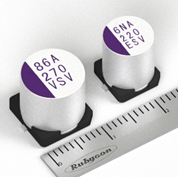
Tables 2 and 3 show a comparison of the specifications of the PSV Series and conventional products.
With the improved heat resistance and ESR performance, the PSV Series has made it possible to maintain stable ESR characteristics for a long period of time even when it is used in high temperature (Figure 4). It guarantees the industry’s top-rated ripple current that is 1.5 times of the ripple current of the conventional product (PHV Series). Furthermore, the standard value of ESR after the durability test is set as the value same as the initial ESR standard of conventional products.
As a result, it is possible to reduce the size to Φ8 products where Φ10 products are conventionally used due to the constraint imposed by the ripple current. In addition, it is possible to contribute to equipment’s miniaturization and weight reduction by reducing the number of capacitors when multiple capacitors are required.
Temperature range | -55ºC ~ +135ºC |
---|---|
Rated voltage range | 25V ~ 63V |
Capacitance range | 33µF ~ 330µF |
Product size | Φ8×10.5L ~ Φ10×10.5L |
Durability | 135ºC 3,000hours |
Over-temperature guarantee | 150ºC 300hours |
Moisture resistance | 85ºC85%RH 2,000hours |
Table 2: Main specifications of PSV Series
PSV Series (developed product) |
PHV Series (conventional product) |
||
---|---|---|---|
Temperature range | -55ºC – +135ºC | -55ºC – +135ºC | |
Rated voltage-Rated capacitance | 35V 270µF | 35V 270µF | |
Case size(ΦD×L㎜) | 10×10.5 | 10×10.5 | |
Rated ripple current(135ºC,100㎑) | 3000mArms | 2000mArms | |
Initial ESR(MAX) | 20ºC 100kHz | 16mΩ | 20mΩ |
-40ºC 100kHz | 13mΩ | (no setting) | |
ESR after durability test(MAX) | 20ºC 100kHz | 20mΩ | 40mΩ |
-40ºC 100kHz | 17mΩ | (no setting) |
Table 3: Comparison of specifications with conventional products
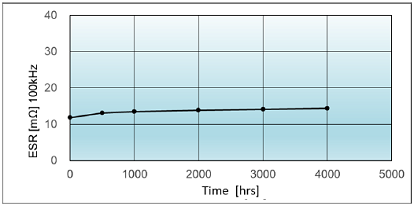
Considering the use in a low-temperature environment, such as in cold climates, the ESR specifications of -40ºC and 100kHz have been set both before and after the durability test. Electrolytic capacitors used for the in-vehicle equipment may suffer from significant changes in their electrical characteristics at low-temperature environments and near the end of their lifetime. Therefore, there is a tendency to select over-specified capacitors by increasing the size beforehand.
The PSV Series has excellent lifetime characteristics at high temperature and follows ESR standards before and after the durability test. This enables wide selection for the appropriate capacitor. In addition, the series has high moisture resistance and over-temperature resistance, making the series optimal products for in-vehicle devices used in a wide temperature range.
Future Development
As described in the preceding sections, the conductive polymer capacitor (hybrid) features low resistance, high ripple cur-rent, outstanding temperature characteristics, and durability. Therefore, its use has already started in every equipment.
In automotive applications, in particular, the 48V mild hybrid system, which is being developed mainly in Europe, has become popular, and the conversion of high power applications, which do not use electricity, to electric will advance. Therefore, the demand for high-performance capacitors will grow more than ever. Also, the development of safety functions and automatic operation will cause huge expansion for various sensors. As a result, the number of capacitors to be mounted is expected to drastically increase.
Compact high-power capacitors are used not only for auto-motive equipment, but for varieties of other equipment. In fact, their usage is expanding in portable home appliances and electric tools requiring miniaturization, outdoor communication equipment requiring high reliability, and lighting equipment. In order to respond to these market demands, the company will continue to improve its original hybrid technology. It will continue to enhance the product lineup by increasing the size variation, increasing the capacitance, lowering resistance, in-creasing allowable ripple current, increasing operational temperature, increasing resistance to high-voltage, and others.
*This is an article which was published in the column of High Technology in Dempa Shimbun published on 24rd January 2019.